By Joe Gresh
I bought the 2008 Husqvarna SMR510 in 2009. I forget the exact mileage on the bike but it was around 800-ish, I think. The Husky was essentially a new motorcycle and the bike sat very tall for a guy with stubby legs. The seat height wasn’t my biggest problem though, the real issue was the diabolical kickstand the manufacturer cursed the Husky with.
The stand was both too short and angled wrong so that when deployed its contact point was only a few inches left of the centerline of the motorcycle. On the stand, the bike would lean way over, unloading the rear suspension to the point the rear wheel was nearly off the ground. This meant the bike fell over a lot. The slightest breeze would pivot the bike onto the stand and knock the Husky onto its left side.
That’s not all that was wrong with the Husky’s kickstand. The foot of the stand was only a millimeter or two wider than the 7/8-inch steel tube the stand was made from. Parking the Husqvarna on anything other than solid concrete was an iffy proposition. If the bike was on sand or dirt the stand would punch through the ground and the bike would fall over. I learned that in the dirt you had to lean the thing against a tree if you wanted to park.
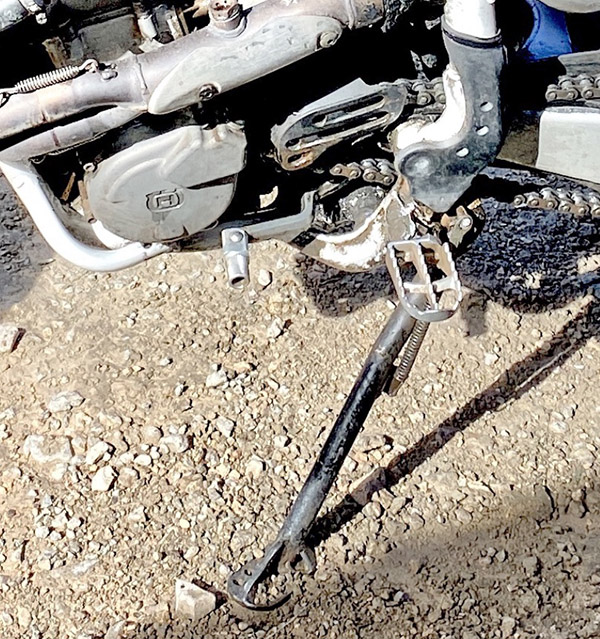
One of the first things I did to the bike was add a gigantic chunk of steel to the bottom of the stand in order to spread the load a bit on soft terrain. I angled the new foot outboard, effectively moving the contact point an inch further from the centerline. The new foot also moved the contact point forward a bit to help even out the fore-aft balance. It kind of worked. The bike fell over less but it still fell over.
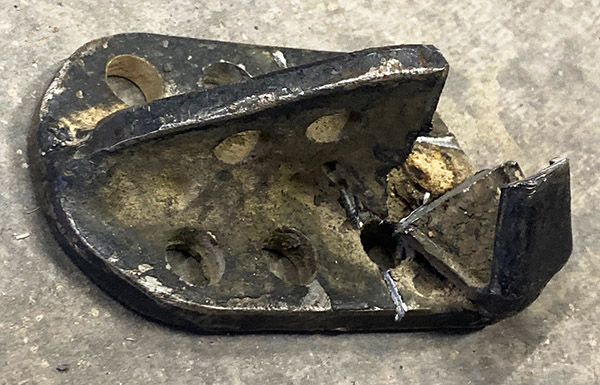
The SMR510’s high seat was a pain to climb onto so I decided to raise the rear shock bolt about ½-inch which lowered the back of the bike a full inch. Now I could reach both feet to the ground on tippy-toes or one foot flat. The lowering also improved the kickstand angle and stability although it caused trickle-down issues.
The Husky is blessed with an ultra plush rear suspension. The bike is a Cadillac on rough dirt trails. With the shortened ride height the bike leaned less on the stand in fact it was almost too vertical. Now when I got on the bike the rear would sag pushing against the stand causing the bike to lean hard right. To get the stand folded up I had to lean the bike much further to the right like a 45-degree angle so that the arc of the stand-swing would clear the ground. Even if I wasn’t sitting on the Husky to fold the stand up I had to hold the bike well over center. I dropped it a few more times.
Things stayed like this for many years. My method of mounting the SMR510 was to first fold the stand up then swing my leg over the back of the seat, scratching the rear fender with my boot and settle down into the saddle as the suspension sagged and my feet hit the ground. It was an ok system when I was younger and more flexible.
Unfortunately frailty creeps up on all of us over time. The last few years it became harder to swing my leg high up over the rear of the Husky. The pack I keep strapped to the rear fender made the situation worse. I had to change my methodology and begin a more right-angle frontal assault, high-kicking my leg over the seat like a hurdler or John Cleese at the Ministry of Funny Walks.
You can guess how well that worked: to get on the Husky I had to flip the stand up, hold the bars with one hand, step back far enough to give my leg clearance and kick as high as I could while stepping forward into the bike. Most of the time it worked but if you didn’t get your foot high enough it would smack into the seat and push the bike over. The Husky falls well and all, but still. Getting off the bike was no easy feat either. In fact, I dropped the Husky more dismounting the motorcycle than mounting, although it was a close run thing, percentage-wise.
It got to where I didn’t want to ride the Husqvarna because I dreaded getting on or off of the bike. It all came to a head a few weeks ago when the Mud Chuckers and I did a 140-mile pavement loop with a 40-mile dirt section in the middle. We pulled into the café at Mayhill for a lunch stop but the place looked closed. Neither of us actually checked the door because we didn’t want to go through the trouble of climbing off our bikes.
The parking lot at the Mayhill Café has a slight slope to it and I rolled the bike backwards to leave. The Husky wouldn’t start. Nothing. No clicking. The instrument panel and fuel pump energized so I figured something was wrong with the starter motor circuit. I made the fatal error of positioning the kickstand side downhill. I slid my butt off the seat and started to drag my tired leg over the top of the seat Normally not a big problem. The added distance created by the parking lot falling away meant my leg needed to go even higher to clear the seat and the bike began to topple over onto me. I was bunny hopping with the one leg on the ground and the other leg still not clear of the seat. Events rapidly overtook my hop-speed and the bike fell over. Luckily I was still wearing my helmet because when I fell backwards I smacked my new helmet on the asphalt pretty hard. I think I would have cracked my head open otherwise.
As I was lying on the ground with the Husky on my leg I cursed a torrent of bad words, some of them even I didn’t know the meaning of. It was like I was speaking in foul-tongues except the Holy Spirit was not the one doing the talking. We got the bike off of me and picked it up. I told Mike, “I’m not riding that @#@ing motorcycle again until I fix that #$@@-%ing kickstand.” We push started the bike and I rode home. So I guess I did ride it again after all.
The starting problem turned out to be a loose connection at the start relay but to be sure I took all the bodywork off and disconnected all the multi-pin plugs on the wiring harness and gave them each a shot of silicone. I relocated the horn to gain a bit more wiring room behind the headlight and changed the old, crumbling air filter for a new one. The Husqvarna was running fine. Except for that diabolical kickstand.
The main problem with the kickstand is that when deployed it is too close to the centerline of the wheels. The reason for this is the kickstand-mounting lug on the frame is angled wrong. Instead of the stand swinging out it sort of swings down. All of the Husky’s kickstand issues stem from this one critical design flaw.
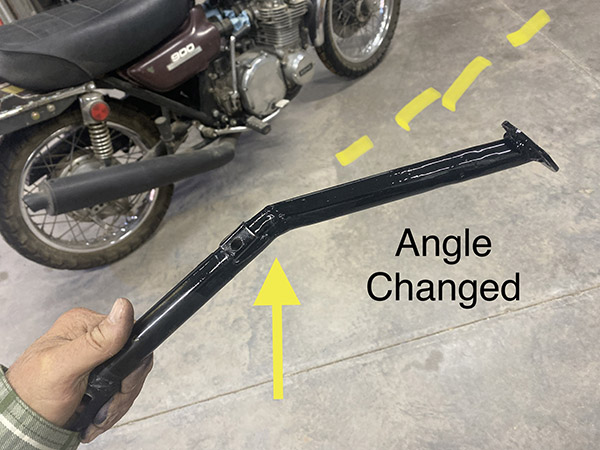
I don’t want to mess with the Husky’s frame so I decided to hacksaw a wedge out of the stand (below the return spring mount) and closed the wedge so that the stand would project about 4 inches further outboard. I welded the join as best I could not being able to see the weld or the seam.
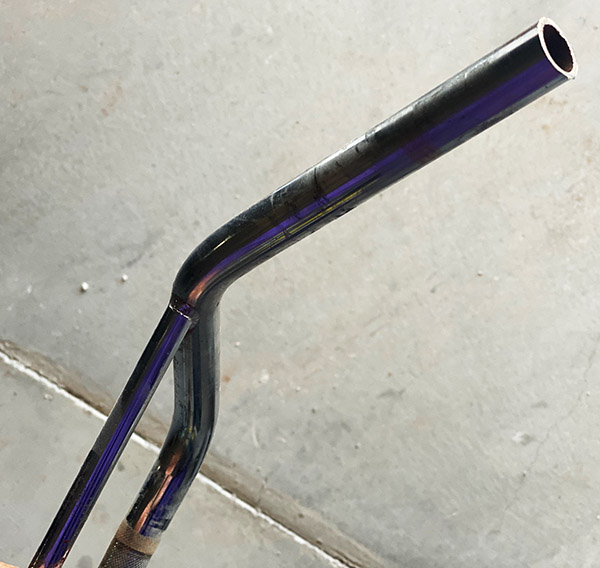
Moving the foot outboard made the bike lean over too far so I borrowed a few inches of tubing from an old Yamaha handlebar to extend the length of the stand.
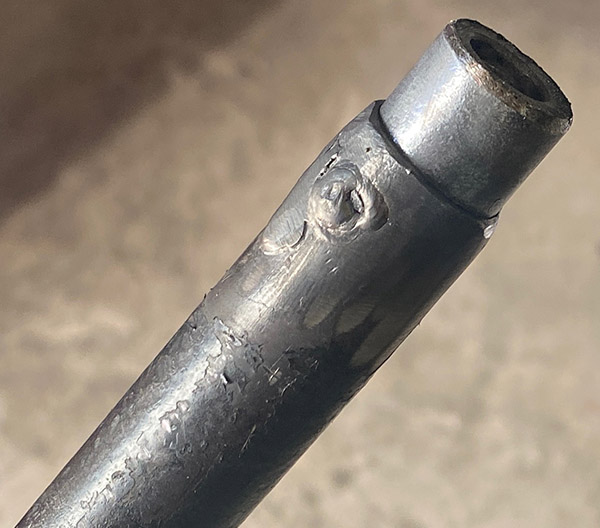
I made a plug to insert into the tubing where the old stand and the handlebar piece join, a couple holes drilled into the tubing allowed me to butt-weld the insert and weld the thin tubing together without burning through.
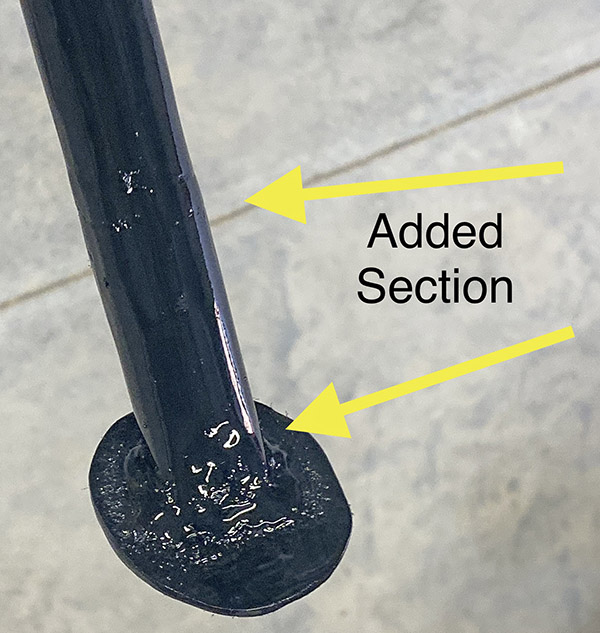
I made a new, lighter foot and cut a new angle on the end of the stand to suit 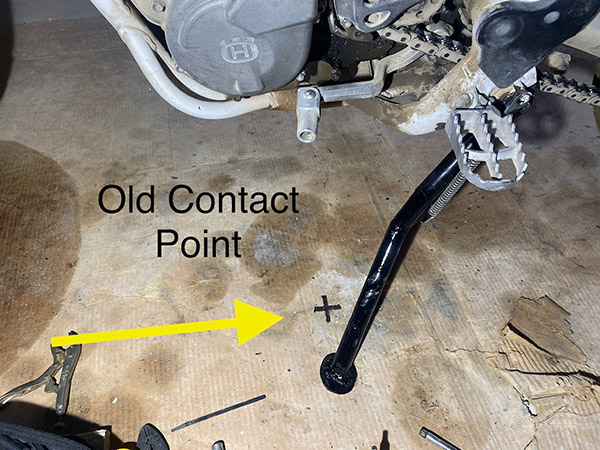
And it is wonderful. Parking the bike is so easy when it doesn’t fall over from the slightest breeze. My new mounting technique (with the stand in the down position) is to put my left foot on the peg, grab the bars, stand on the foot peg, swing my leg easily over the rear pack, settle down into the seat and with my left foot, swing the stand up. Easy-Peasy. It sounds like I should have been able to do this all along but the geometry just didn’t work that way.
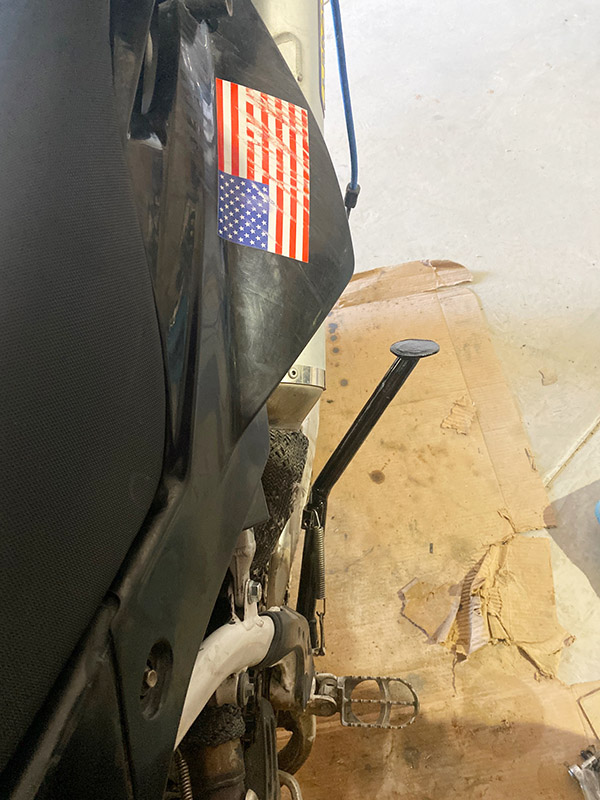
Putting up with the old kickstand for 14 years shows how a bad idea can keep loyal followers. It took that hard fall In Mayhill to jar me into action. There is no free lunch, however. The new stand angle awkwardly juts out from the side of the bike and will most likely break when I crash on that side. I’m hoping my shoddy welding will be like a fuse and it will break at the join before something important breaks.
The kickstand mod has made me fall in love with the Husqvarna again. It’s such a light, powerful bike you feel like there’s not much you can’t do with it. Now that I can easily get on and off the bike those feelings of dread are distant memories.
I’ll see you on the trails.
More motoliterature from Dos Joes? You bet!
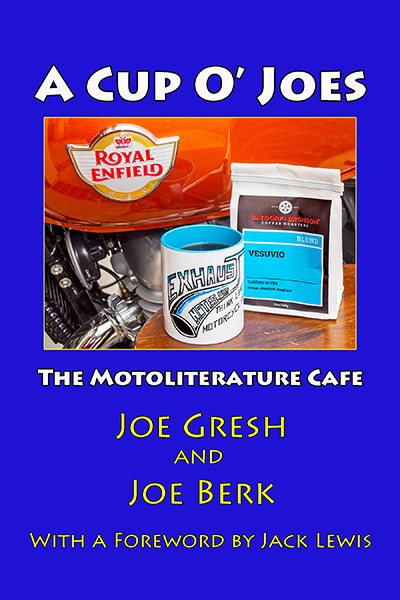
Never miss an ExNotes blog:
Don’t forget: Visit our advertisers!
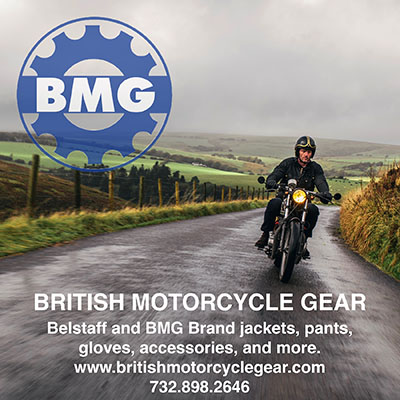
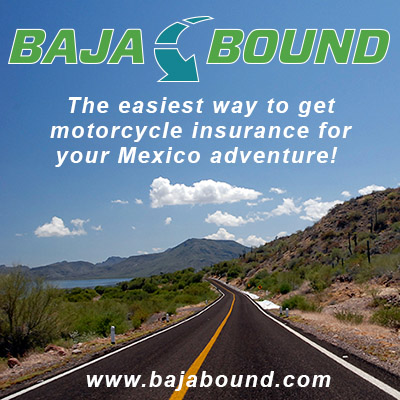